Appearance
Knock Out v1 + v4 (Patent Pending Robot – FTC 11285) | Sohm - 11285
This is the CAD for FTC Team 11285 PATENT PENDING’s robot, Knock Out, available as a Onshape Link.
It features a pass-through design commonly used in FTC and serves as a great source of inspiration for rookie teams looking to design reliable and competitive mechanisms.
Drivetrain
Featuring a parallel plate dead axle mecanum drivetrain, it stands relatively small at roughly at 13in x 14in. It consists of 3 gobilda 4bar odometry pods for autonomous, and more impressively, an overcentering linkage for a power takeoff (PTO). (PTO available in different tab). The drivetrain also features a limelight 3a for autonomous sample detection/intake, and uses magnetic limit switches to determine whether the vertical and horizontal slides are fully retracted (determine robot's ready for transfer)
Vertical Lifts
Using two 5 stage linear slides (misumi sar230) these high speed lifts are strung continuously and are powered by 2 gobilda 1150 rpm motors. In addition, the lifts are countersprung using bungee cords making the deposit assemble nearly weightless to the motors. (Inserts available in a different tab)
Depos
An arm powered by 2 swyft balance servos and the wrist powered by an axon mini, the deposit assembly is designed for high speeds. The long arm allows for the robot pick up specimen off the field wall to place them on the high chamber without needing to rotate the robot. The depos assembly also consists of 2 spring loading hooks for the level 3 hang. This assembly features 2 ELC analog encoders to get real time positions for the joints without needing to account for gear ratios (more accuracy)
Intake
This active intake on a 3 stage extendo (sar230), it is able to grab samples for almost anywheres in the submersible. The intake is pivoted by 2 axon maxs and powered by a gobilda 1620rpm motor. This allows the intake to have a "touch it, own it" mentality. The intake also features a color sensor for sample detection and springloaded top cover to prevent samples from falling out. This assembly featurs 1 ELC encoder on the pivot.
Hang
This level 3 hang uses a 2 step process to complete it. First, 2 spring loaded arms above the parallel plate will grab the lower bar for the level 2 hang. Powered by 4 axon maxs, the robot should have no trouble getting up. After that, the vertical lifts will extend and the spring loaded hooks on the depos will grab the high bar. The PTO will engage, temporarily redirecting torque from all 4 drive motors to the vertical lifts. This 6 motor hang will quickly lift the robot from level 2 to level 3. The triangular shape of the parallel plate will allow the robot to pivot around the low bar during the l2 to l3 transition
Advantages
- Effective pass-through design for efficient transfers
- Integrated autonomous-friendly mechanisms (Limelight + odometry)
- Counter-sprung lifts reduce motor load
- Mechanically consistent depos system
- Compact but capable drivetrain layout
Download & Access
The Onshape link for Knock Out:
View/Download Here (V1)View/Download Here (V4)
WARNING
Although this robot has been tested in a real season, slight CAD inconsistencies may exist. Please check and adjust the model as needed before using it in competition.
Version 1 Photo:
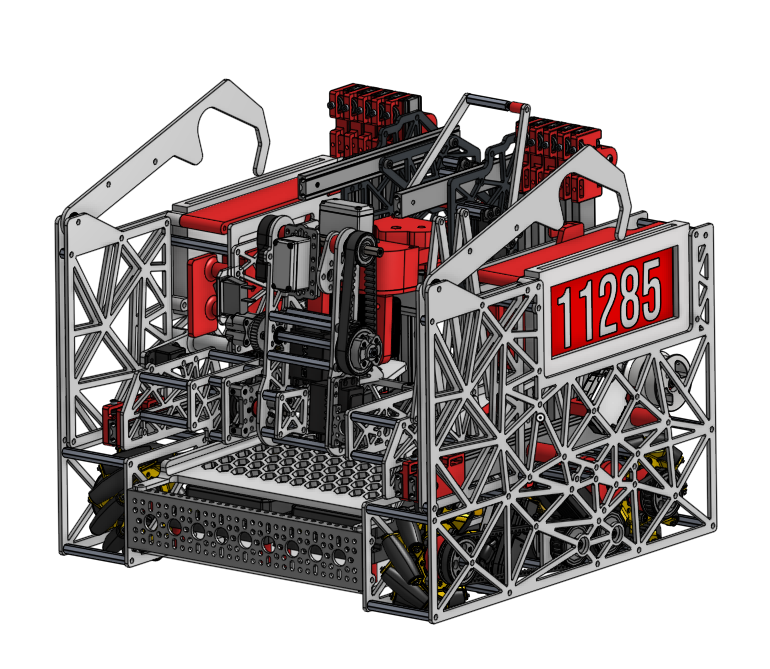
Version 2 Photo:
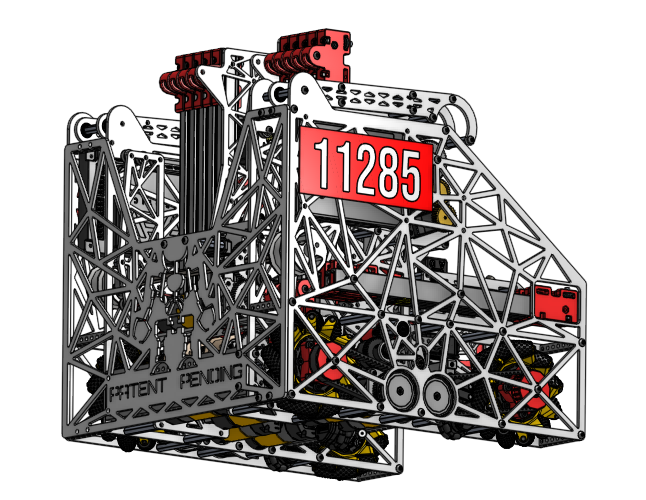